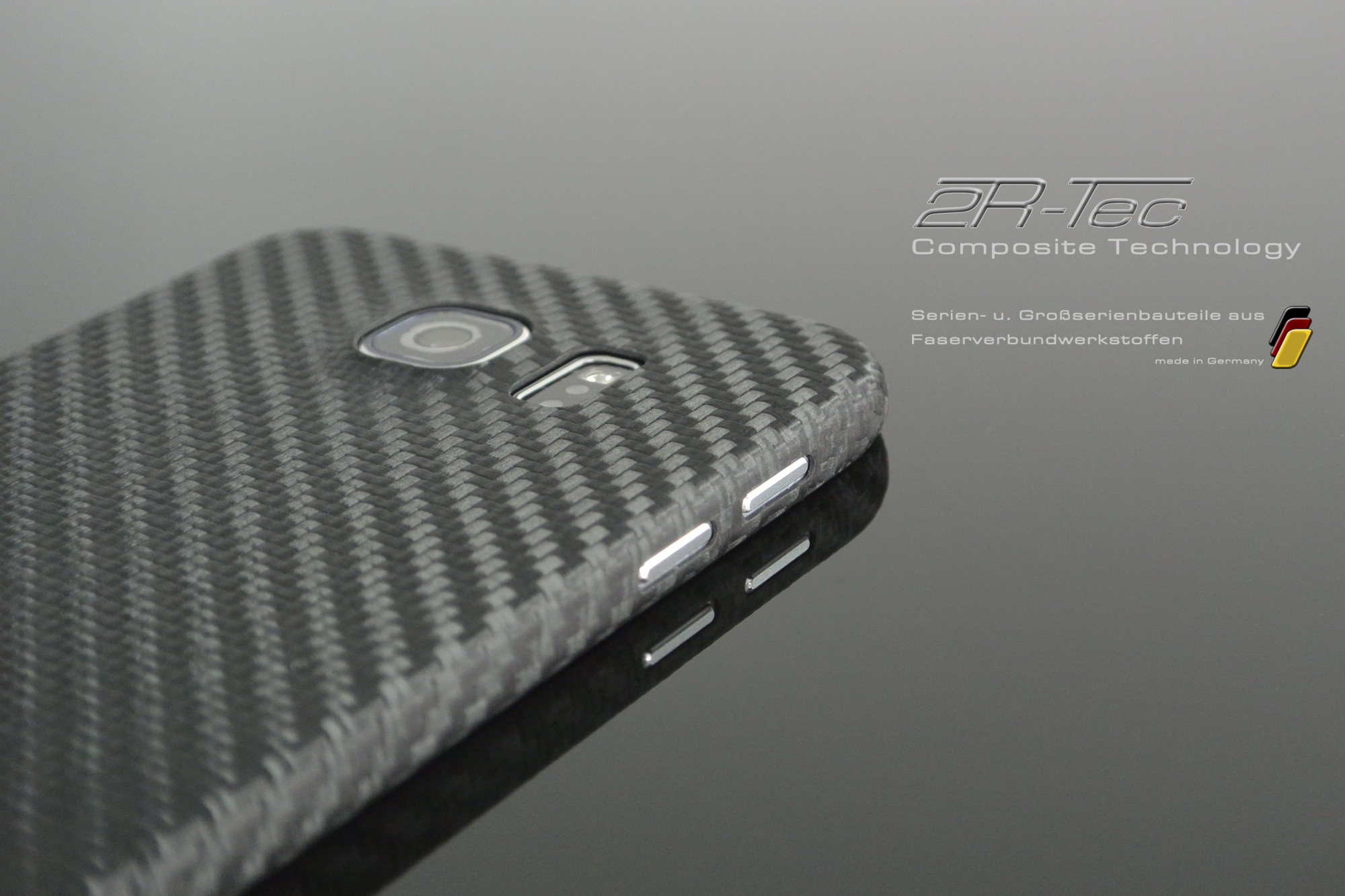
2R-Tec Composites
Batch and high volume component parts
of fiber-reinforced composites
The Company
Main business focus of 2R-Tec GmbH & Co. KG is the batch and high volume production of component parts of fiber-reinforced composites on the basis of recyclable thermoplastics and highly reactive thermosetting plastics.
A large in-house production depth reaching from layout of part, design of forming tool, tool construction, batch production of the fiber-reinforced composite parts up to surface refinement makes it possible to react in a flexible and contemporary way in almost each and every process step.
An up-to-date plant for processing of fiber-reinforced composites – together with our rapid forming procedure – facilitates an efficient batch production of large volumes and gurantees
highest quality resulting in a great advantage for our customers to develop new markets with these light, reinforced composites.
It is our target to develop, by constant improvement, more efficient manufacturing procedures with reproducible processes for batch production of component parts of fiber reinforced composites with thermoplastics and highly reactive thermosetting plastics as matrix.
In this connection we can lean on many years of experience in the field of fiber treatment, plastics technique, mould and fixture design and construction.
2R-Tec is resident in Germany, approx. 100 kilometers north of Frankfurt/Main, in Dautphetal (Hessen). This idyllic region is a stronghold of mould and tool design and construction as well as plastics processing for the automotive industry.
We invite you now to get a comprehensive idea of our company and the great variety of possibilities we can offer on our new website.
2R-Tec GmbH & Co. KG
Administration and Technical Center
Hornweg 4a
35232 Dautphetal
Telefon: +49 (0)6466 / 911 4-66
E-Mail: info@2r-tec.de
Series Production
SERIES PRODUCTION
Mass-produced reproducible quality
Optimum and controlled manufacturing conditions belong to the production of high-quality composites.
Beside the controlled machine and tool data such as cavity pressure measurings etc. parameters as dust content, humidity and temperature are only some of the process monitored sizes which are required as frame conditions for reversible manufacturing conditions in batch and large volume production.
In optimum conditions we produce composites on continuous, linear production lines with specially developed processes guaranteeing batch sizes of more than 100.000 pcs/year. according to component part.
Medium batches > 10.000 pcs./y
High volumes > 100.000 pcs./y
Quality
DEVELOPMENT
Higher • quicker • further - we are constantly developing
More and more new tasks and demands on material of the component parts and the production processes require permanent development work.
Whether chemical or mechanical tests, we try to reach the optimum in quality and process flow with respect to the necessary sizes.
Design
DESIGN
CAD/CAM design with control
With most up-to-date CAD systems we design component parts, forming tools and devices required for batch production. Conversion of CAD data into machine data (CAM) with control and comparison of the component part tolerances guarantees slightest deviations of your specified values.
3D Digitalization
3D DIGITALIZATION
3D scanning – quick making out of data
3D scanning facilitates quick and flexible digitalization of dimensions of models, tools, prototypes and many other objects formed as you like, independent of type of material in real time.
As contactless procedure the 3D scanning provides the exact data of the component part geometry.
Size of the part to be scanned can be from 1 mm up to 10 m. For comparison of tolerances, volume models can be compared with these data with CAD design data or even new forming tools and models can be made out.
Model Design and Construction
MODEL DESIGN AND CONSTRUCTION
A model always pays off
Essential parts from planning up to batch production are models and prototypes
which already pay off during the first meeting.
In particular in case of developments where weight and stiffness are important there can often be observed an excess in material. If this is eliminated the STW value (stiffness-to-weight) can still be improved.
Fixtures required for batch production (e.g. for treatment, storage, paintwork and transportation) belong to the scope of the model and fixture design and construction.
Functional models, illustrative models of aluminium, plastics or composites such as carbon etc.
Gauges for control during running production
Zero-point clamping fixtures for mechanical treatment
Linear guides and drives for series processes
Painting devices, fittings
Mechanical Treatment
MECHANICAL TREATMENT
Component part treatment – precision makes the difference
Treatment of fiber-reinforced composites requires use of different treatments according to type of fiber and demands a lot of the cutting tool, the clamping fixture and the machine.
Special zero-point clamping systems guarantee reversible, precise treatment and quick change of clamping tools.
Multi-axle simultaneous CNC treatment
Pure waterjet cutting
Lasing
Blanking
Edge and surface treatment
Surface Refinement
SURFACE REFINEMENT
The finish matters
Different coating processes and paint systems are used based on surface requirements and batch size.
In-mould coating IMC
Coatings based on water lacquer
Solvent reduced paint systems
UV-hardening lacquers
For larger volumes the reversible process of dip-coating with UV paints which have an outstanding scratching resistance is an ideal coating solution with extremely short cycle times.
In case of small and initial batches as well as prototypes or big component parts up to a lot size of 300 pcs., application of paint by hand in a spray process should be favoured.
Topics:
Direct coating in heated forming tools with in-mould coating
Coating of large volumes in spray process or dip coating
Labeling by pad printing in case of serial parts
Painting by hand (spraying) of small and initial batches
Applications
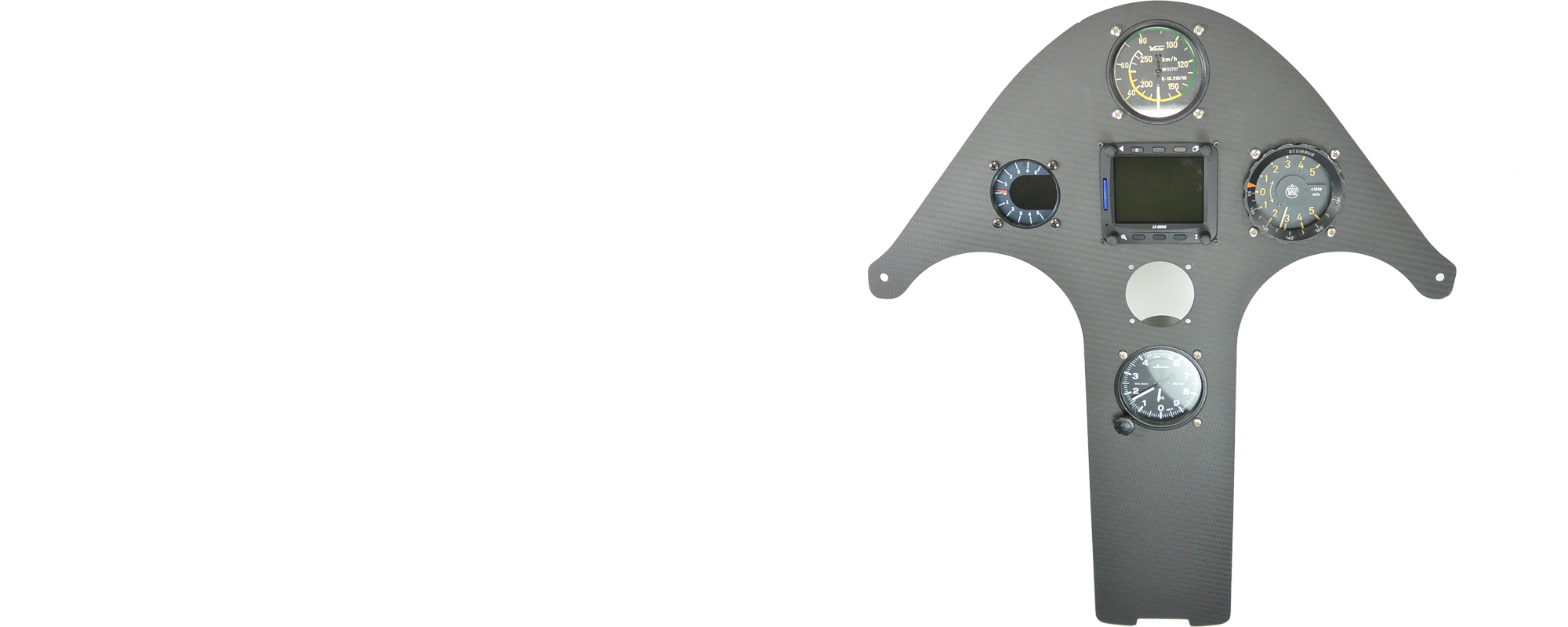
Automotive engineering and vehicle construction
(parts for interior and exterior, fuel cells)
Aerospace
Alternative energies (wind power, photovoltaics, fuel cells etc.)
Mechanical engineering (all types of machines, measuring technique etc.)
Medical engineering (devices, X-ray equipment, orthoses etc.)
Electronic industry (housings and covers of appliances, cables,
boards, batteries, energy stores etc.)
Sport industry (sport equipment and accessories etc.)
Lifestyle industry (suitcases, writing utensils, frames for eyeglasses etc.)
Military sector (vehicle parts, antiballistic clothing etc.)
Building industry (carbon concrete, bridges, statically load-bearing parts and profiles)
Rapid-Forming

Rapid Forming
High speed – in manufacture of composites
The rapid forming process is a process optimized regarding flow and cycle
time for the production of fiber-reinforced parts of medium and large batch sizes.
In optimum conditions of process, component and forming tool up to several thousand
composite parts can be produced a day.
In case of large volumes use of variotherm forming tools made of steel with automatic
ejector equipment etc. is required.
These variotherm tools are normally heated via induction and cooled back to the
demoulding temperature with a liquid or gas cyclically to forming process.
The extremely fast hot/cold cycle is the advantage of these very special tools.
An optimized and automatic production line from precise CNC pre-cut of the
technical fabric, transportation of the fabric and the actual fully automatically controlled
forming process is guarantor for reproducible production processes and high
quality components made of fiber-reinforced composites.
Enviroment
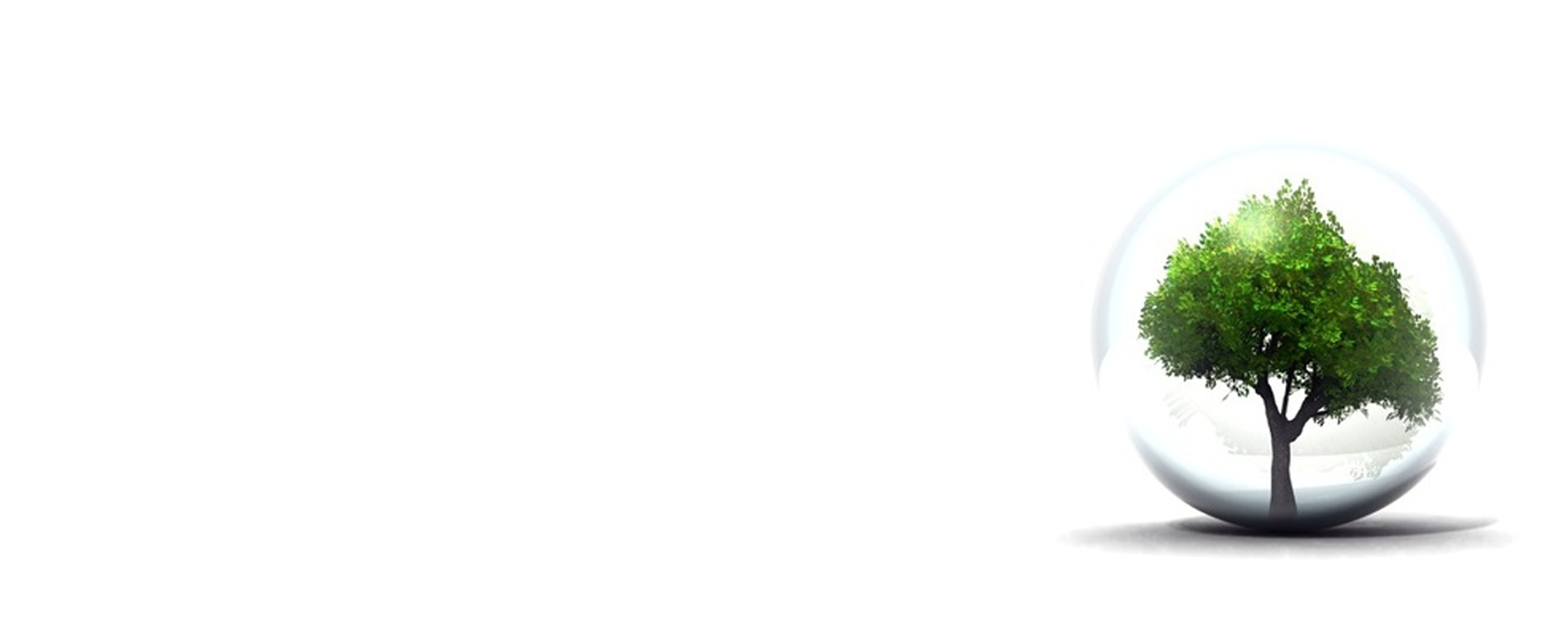
Environment
Ecological and economic advantages
Important aspects for the future are the ecological and economic points of view
and the protection of raw material and resources which become more and more
important even because of legislative initiatives (reduction of CO2 emission).
For the process chain from the raw material carbon which is available nearly
indefinitely to the finished carbon component only approx. 25 % of power
is required compared to the similar part made of steel.
In addition comprehensive and environment damaging antioxidation processes,
e.g. galvanizing in electrolytic bath, are not needed.
Also the decreasing energy required for motion of lightway construction parts,
used for example in vehicles, has a positive result on the total energy balance thus
resulting in a significant reduction of the operating costs.
A current example is the new Boeing „Dreamliner“ 50 % of which consist of carbon
and needs17 to 20 % less fuel due to the weight saving.
Maintenance costs will also be reduced by approx. 15 % by use of composite materials.
Topics:
Suitable for large batches, but made-to-order
Favourable continuous production lines
Material which improves the products